Empowering Student Innovation: 3D Scanning the Ind-E Capstone Vehicle with Rapid 3D and BCIT
- 3dinfo2
- 1 hour ago
- 4 min read
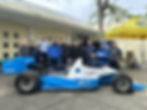
A team of BCIT engineering students is taking electric vehicle design to the next level with their final capstone project, the Ind-E Project. Their goal: redesign and upgrade a vintage IndyCar from its original combustion powertrain to an electric powertrain using acquired engineering knowledge and advanced 3D scanning.
Driving Collaboration Through Advanced Measurement Solutions
Every great engineering project starts with a big idea and a big challenge. For the students behind the Ind-E Capstone Project at the British Columbia Institute of Technology (BCIT), that challenge was clear: design and integrate complex mechanical and electrical components into an electric powered IndyCar. But before a single bracket could be mounted or adapter plate fabricated, one critical task had to be completed: accurate measurement.
From frame geometry to motor mounts, the Ind-E team needed precise references to develop CAD models, design components, and document the vehicle assembly. Manual measuring methods would have been time-consuming and error-prone, especially given the project’s complex geometry and multi-disciplinary scope involving both mechanical and electrical engineering students. That’s where Rapid 3D stepped in to help.
From Concept to CAD: A Scanning-First Approach
Rapid 3D partnered with BCIT to scan the Ind-E vehicle, capturing everything from structural members to tight bolt-hole patterns using our Canadian made portable 3D metrology-grade scanners from Creaform.
Right Tool for the Right Scan
To ensure optimal results, we used three different Creaform 3d scanners:
HandySCAN MAX Elite, for scanning large components like the monocoque/chassis and body components.
HandySCAN Black Elite, for detailed features and small-volume components, such as adapter plates and tight-tolerance flanges.
MetraSCAN BLACK, deployed during the final scan session for a full-vehicle assembly scan. This scanner offered excellent accuracy and repeatability across the complete vehicle


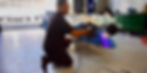
This multi-scanner strategy gave the students high resolution and sub-millimeter accuracy from every angle, allowing them to handle both micro and macro design needs across the project. Replicating the geometry and surfaces with hand measurements to create reference models in SolidWorks would involve lots of assumptions which could negatively affect the project. One example of this was the original fuel cell envelope. The students initially took manual incremental measurements of the fuel cell envelope so they could design a new accumulator container (i.e. battery pack) to fit in the space. Their initial design ended up being too wide.
Using scan based design, they were able to virtually fit the accumulator assembly in the scanned fuel cell envelope. They were able to see the issues with the initial design that was based on their manual measurements. They found that the container was 8mm too wide at the front. Therefore with accurate 3D measurements, they were able to revise their design of the accumulator container to fit inside the fuel cell envelope without issues.

From Scan to Solution: Reverse Engineering in Action
With precise scan data in hand, the Rapid3D team used Creaform.OS Scan-to-CAD Pro to convert complex scanned components, such as the adapter plates, directly into accurate CAD models. The software was instrumental in extracting detailed features like bolt hole patterns from the mesh and using as-built design principles to create a CAD model ready to use for designing new parts. These precise measurements were then seamlessly transferred to SolidWorks, enabling the team to integrate the components confidently within their vehicle assemblies. Scan-to-CAD Pro is not only convenient, it is an essential problem-solving tool when working with scan data.


How 3D Scan Data Solved Real Engineering Problems
Fixture Design Accuracy: The scan enabled students to align CAD models of their custom vehicle jig with the actual chassis geometry. This ensured secure and accurate support for the vehicle during testing and assembly.
Precision CAD Modeling: Scanned geometry was used to digitally reconstruct key structures such as the carbon-fiber monocoque and rear transaxle. This allowed the team to simulate fitment, verify tolerances, and avoid repeated manual measurements.
Load Bearing Member (LBM) Fitment: The scan ensured that the custom-built LBM could restore structural continuity between the monocoque and transaxle, maintaining precise alignment across mounting points.
Assembly Conflict Resolution: The digital twin was used to proactively identify interference issues. For example, it helped prevent physical clashes between the sidepods and motor mount components, allowing the team to refine their design before fabrication.
Time Savings and Risk Reduction: Students reported saving dozens of hours on measurement tasks. More importantly, they reduced the likelihood of manufacturing errors and rework by designing components based on accurate, real-world geometry.

Final Scan, Real Results: Full Assembly and Student Feedback
After individual scans were complete, Rapid 3D performed a full assembly scan of the Ind-E vehicle. The result was a complete digital twin of the student-designed cart, accurate to sub-millimeter tolerances.
What the Students Said:
“We saved dozens of hours not having to manually measure and re-check parts.”
“The scan-based CAD allowed us to fully utilize the available space in the frame.”
“Having reliable measurements meant we could move forward confidently with manufacturing.”


What’s Next
This project is just the beginning. As the Ind-E vehicle evolves, BCIT students plan to continue refining the design and potentially enter competitions where performance and precision are key. With Rapid 3D’s support, they now have a solid digital foundation for iteration, innovation, and success.
Ready to take your project to the next level with precision 3D scanning and reverse engineering?
Contact Rapid3D Ltd today to learn how our advanced 3d scanning solutions can empower your team to design smarter, faster, and with unmatched accuracy.